Design for an early Construction Start
- Shift2Lean
- May 25, 2018
- 5 min read
In last weeks article we explored why we need to get "Back to the Future with a Master Builder Approach" and how that lead to strong customer relations and business success. What I didn't tell you was that the next day I stayed over and attended a Seattle Community of Practice meeting and joined Jack the Master Builder for the Target Value Delivery kick-off of a third 45-story Amazon tower.
Communities of Practice (COP's) are a great opportunities for networking and learning. It was interesting to see that our cousins south of the boarder were experiencing a big brother non-lean bureaucracy burden as the COP's finances and approvals need to be coordinated by LCI. In Canada our COP's are more organic, non-profit and easy to start and manage. The Saskatoon COP that we started is one of the most active and used as a model as to "How to KickStart a COP" an article I wrote for LCI-Canada.
Next on the agenda was lunch and then off to our pre-construction kickoff meeting. One of the interesting things I learned while hanging out with Jack the Master Builder is how the team is lean BUT don't use all the lean jargon and that minimizing waste, improving productivity and optimizing work flow are just embedded in the DNA of how they do business. I was so impressed with Jack's team and there approach to kicking off a project that I convinced him to help me deliver Target Value Delivery workshop at our LCI-C conference in Vancouver.
The pre-construction kick off meeting was excellent as it addresses three main pain points that were listed in a recent article "Embracing Failure as a Driver for Change".
We often don't have a clear definition of the project requirements.
Poor design documentation and it's becoming worse instead of better
The design team took way to long on the front end of the project and squeezed construction into a shorter time frame.
We need a Clear Target: What are the real Project priorities?
As an experienced Owner, Amazon are very clear on their project success criteria. We want fast, we want quality, we want minimal changes and we want it at a lean construction cost. This demanding repeat client recognizes that lean project delivery when delivered by a Master is a system for optimizing project value.
In our Shift2Lean Target Value Delivery workshops our first simulation involves weeding the garden to uncover the truth. What really needs to grow out of this project and what needs to be separated into nice to haves and maybes so that the team has flexibility in finishes, functionality and systems choice to hit the almighty clearly defined TARGET COST.
When we design for early construction start it always amazes me how close we can get to the target cost with just napkins, conversations, schedules, schematics and COWBOY math.
Cowboy Math is a desired skill for all members of the design team. It is the ability to produce estimates with minimal information on the fly so that decisions can be made to keep the project moving forward.
Design for Construction, Not Tender - There is a Big Difference
A key innovation in the Sellen approach is how to improve the quality of the design documents by having the people doing the work, develop the construction drawings. This is achieved by having the design team develop to the schematic design phase only and then turning it over to the subcontractors to develop the construction drawings.
This process eliminates the waste associated with developing designs for tender as opposed to what we really want, fully coordinated construction drawings. Drawings with the level of detail that enable contractors to prefab up to 60% of the work off site where it is significantly more productive to build. The IDEA of having the builder develop the Construction drawing is also the preferred way for Kelson Construction a mechanical design-build firm in Toronto. The have a complete BIM shop so they can design to prefab and also minimize interface issues and the costs associated with changes and delays in the field.
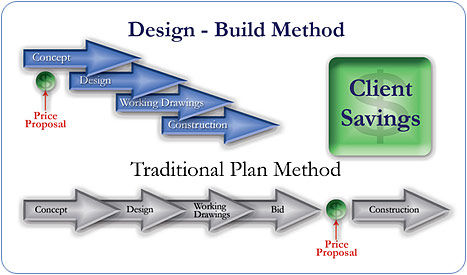
Design for an Early Construction Start
The AHA moment of the trip was how Jack manages the design team to enable an early construction start. The first priority being to align the project team on the design priorities required to get the foundations in the ground early. When you really think about it, great planning right at the start can buy you 3 months of construction time. This is BIG VALUE!
The kick-off meeting would best be described as getting the whole team on the Same Page and prepared for the design pull planning session, that was scheduled for the following week.
Kick Off Meeting Purpose
To validate/adjust and add detail to the design schedule so we can all agree on a schematic thru design development schedule
Identify any constraints and issues that need to be addressed
Collaborate on the best way forward and establish buy-in for a common plan and schedule
Agenda
Introductions
Review of Pull Planning and Weekly Coordination meeting process
Milestone Definition: What is included in this phase of work, roles and responsibilities for design, permitting, zoning approval, estimates and procurement
Work Breakdown: Brainstorm on how this team will communicate, collaborate and share information. What is the most efficient way be productive in delivering this phase of work?
Identify issues and constraints such as permitting regulations that need to be considered.
Plan for the Pull Plan Session: Who/When/Where, what is the work sequence, come prepared with sticky notes defining tasks and be prepared to post in sequence from the end milestone
Plus/Delta
What we learn from the Sellen process is that clearly defined Owner's Project Requirements provide the VALUE milestone for team success. In the case of the Seattle Block 18 project the requirement of an early start was a driver for a streamlined design process.
Next we learned that design to build is different than design to tender and a better process is to have the contractor take over at the schematic design phase. This process has many benefits in that contractors like Kelson Construction can design for ease of construction, designs are not always custom, work is coordinated properly in BIM models to enable prefabrication.
Finally work needs to be delivered Just-In-Time to achieve the right sequence of work flow to get a jump on construction.
It's amazing what we learn when we get out on a GEMBA walk .... How to implement brilliant systems with average people to achieve exceptional results.
Please Connect on LinkedIn so that you don't miss any of the plays needed to contribute to YOUR project success story.
Comments